Introduction to Sandwich Mounts
Sandwich mounts, also known as rubber-metal isolators, are specialized components designed to mitigate vibrations, absorb shocks, and reduce noise in various industrial, automotive, and marine applications. These mounts consist of layers of rubber and metal bonded together, resembling a “sandwich,” which provides their unique ability to balance flexibility and strength.
Structure and Composition
A typical sandwich mount consists of:
- Rubber Layer: Made from materials like natural rubber, neoprene, EPDM, or nitrile, the rubber provides elasticity and damping properties.
- Metal Layers: Steel or aluminum plates reinforce the mount, offering structural stability and easy installation options.
The combination of these materials allows sandwich mounts to isolate vibrations and prevent them from transmitting to other parts of a machine or system.
Key Features of Sandwich Mounts
- Vibration Isolation:
- Sandwich mounts are specifically designed to isolate vibrations generated by machinery. By absorbing mechanical energy, they prevent vibrations from propagating to sensitive components or the environment.
- Shock Absorption:
- These mounts cushion and dissipate impact forces, protecting equipment from damage caused by sudden shocks or loads.
- Noise Reduction:
- By interrupting the transmission path of vibrations, sandwich mounts significantly reduce noise levels in industrial and mechanical setups.
- Durability:
- Manufactured from high-quality materials, sandwich mounts are resistant to wear, corrosion, and environmental factors like heat, oil, and UV exposure.
- Wide Operating Range:
- Sandwich mounts can perform efficiently in a broad temperature range, typically from -30°C to +120°C, depending on the rubber compound used.
Applications of Sandwich Mounts
Sandwich mounts are versatile and find applications across a range of industries, including:
1. Industrial Equipment:
- Machinery Vibration Control: Used in compressors, pumps, and motors to reduce wear and tear caused by constant vibration.
- Generators: Isolate vibrations to ensure stable operation and reduce noise pollution.
2. Automotive Sector:
- Engine Mounts: Absorb vibrations from the engine and drivetrain, improving vehicle comfort and durability.
- Suspension Systems: Provide cushioning in automotive suspension setups for a smoother ride.
3. Marine Applications:
- Boat Engines: Prevent vibrations from transferring to the hull, ensuring quiet and smooth operation.
- Docking Systems: Absorb shocks during docking and loading activities.
4. Construction Industry:
- Heavy Machinery: Installed in excavators, bulldozers, and cranes to enhance operator comfort and equipment lifespan.
5. Aerospace Industry:
- Isolate vibrations in aircraft components, ensuring stability and safety during operations.
Advantages of Sandwich Mounts
- Enhanced Equipment Longevity:
- By minimizing vibrations and shocks, sandwich mounts reduce the risk of component fatigue and structural damage, extending equipment lifespan.
- Cost-Effective Solution:
- Their durability and efficiency reduce maintenance costs and downtime, providing excellent long-term value.
- Improved Workplace Comfort:
- Noise and vibration reduction contribute to a safer and more comfortable working environment, boosting productivity.
- Customization Options:
- Sandwich mounts can be tailored to specific applications, with varying dimensions, hardness levels, and material combinations available.
Factors to Consider When Choosing Sandwich Mounts
- Load Capacity:
- Ensure the mount can support the weight of the equipment and withstand dynamic loads.
- Rubber Hardness:
- The Shore hardness of the rubber layer determines its ability to absorb vibrations and shocks. Softer compounds provide better vibration isolation, while harder ones are suited for heavy loads.
- Operating Environment:
- Consider factors like temperature, exposure to chemicals, and UV radiation when selecting the material.
- Mounting Configuration:
- Options include stud mounts, bolt-through designs, and custom configurations for specific applications.
Maintenance Tips for Sandwich Mounts
- Regular Inspection: Check for signs of wear, cracking, or corrosion on both the rubber and metal components.
- Proper Installation: Follow manufacturer guidelines to ensure secure and effective mounting.
- Environment Monitoring: Avoid prolonged exposure to extreme temperatures or aggressive chemicals to extend the life of the mounts.
Future Trends in Sandwich Mount Technology
With advancements in material science and engineering, sandwich mounts are evolving to meet the demands of modern industries. Innovations include:
- Enhanced Damping Materials: Development of rubber compounds with superior shock absorption and temperature resistance.
- Smart Vibration Isolation: Integration of sensors to monitor and adjust isolation performance in real-time.
- Sustainable Materials: Increased use of recyclable and eco-friendly materials in mount production.
Conclusion
Sandwich mounts play a critical role in ensuring the smooth, efficient, and safe operation of machinery across various industries. Their ability to isolate vibrations, absorb shocks, and reduce noise makes them an indispensable component in modern engineering. By choosing the right sandwich mount and maintaining it properly, businesses can optimize equipment performance, reduce maintenance costs, and create a more comfortable working environment.
If you’re looking for high-quality sandwich mounts tailored to your application, consult a trusted manufacturer to explore the best solutions for your needs.
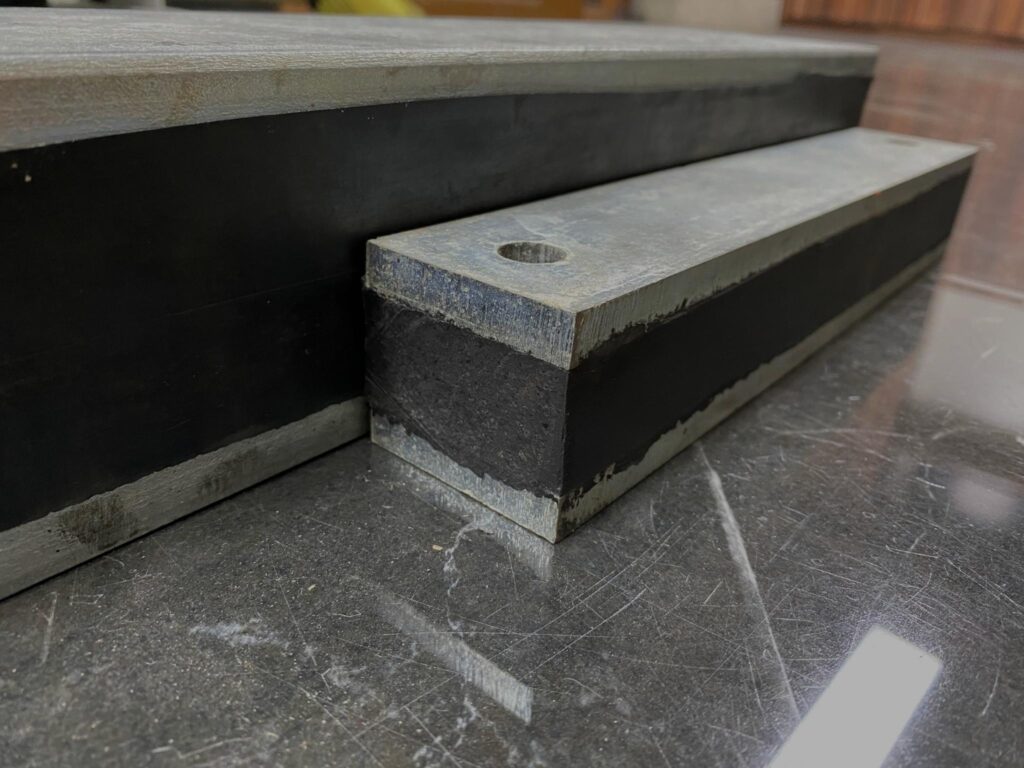
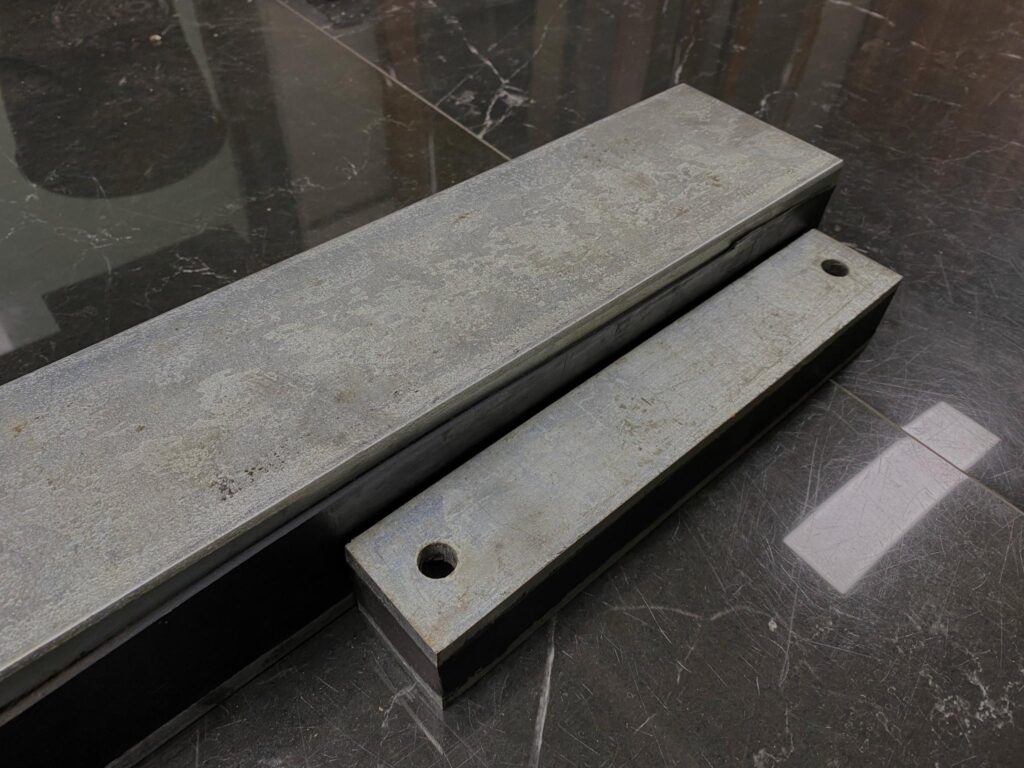
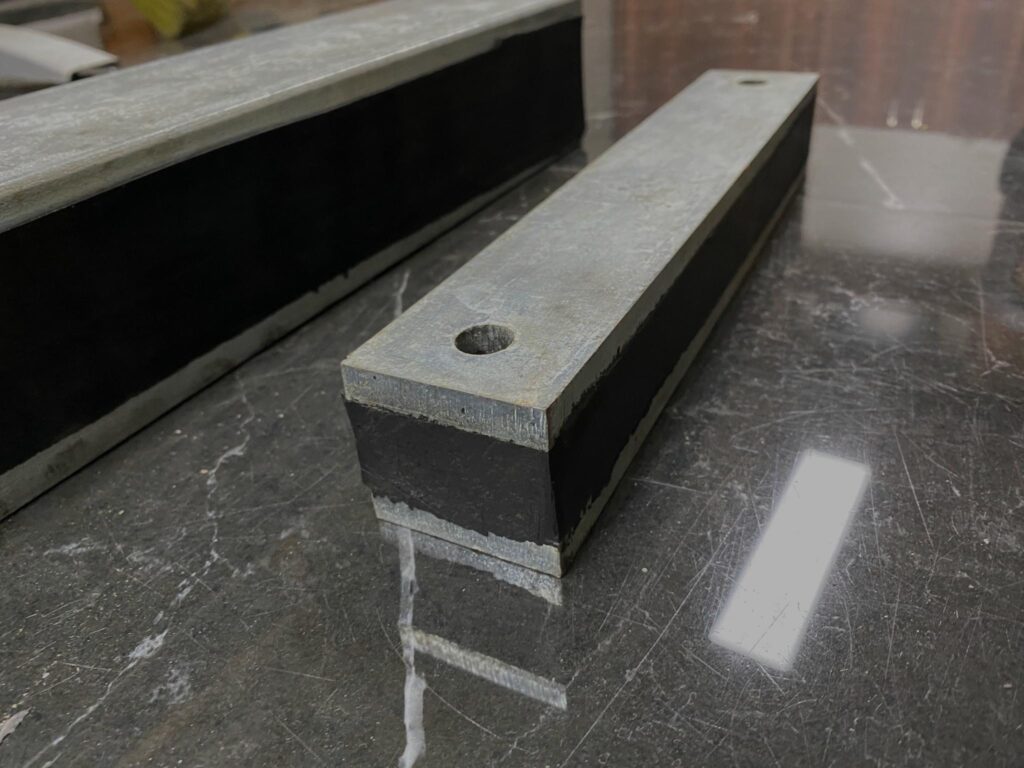